Corona-Schnelltest zum Nachweis von SARS-CoV-2.
Here you can read the sustainability report of TextilPlus GmbH
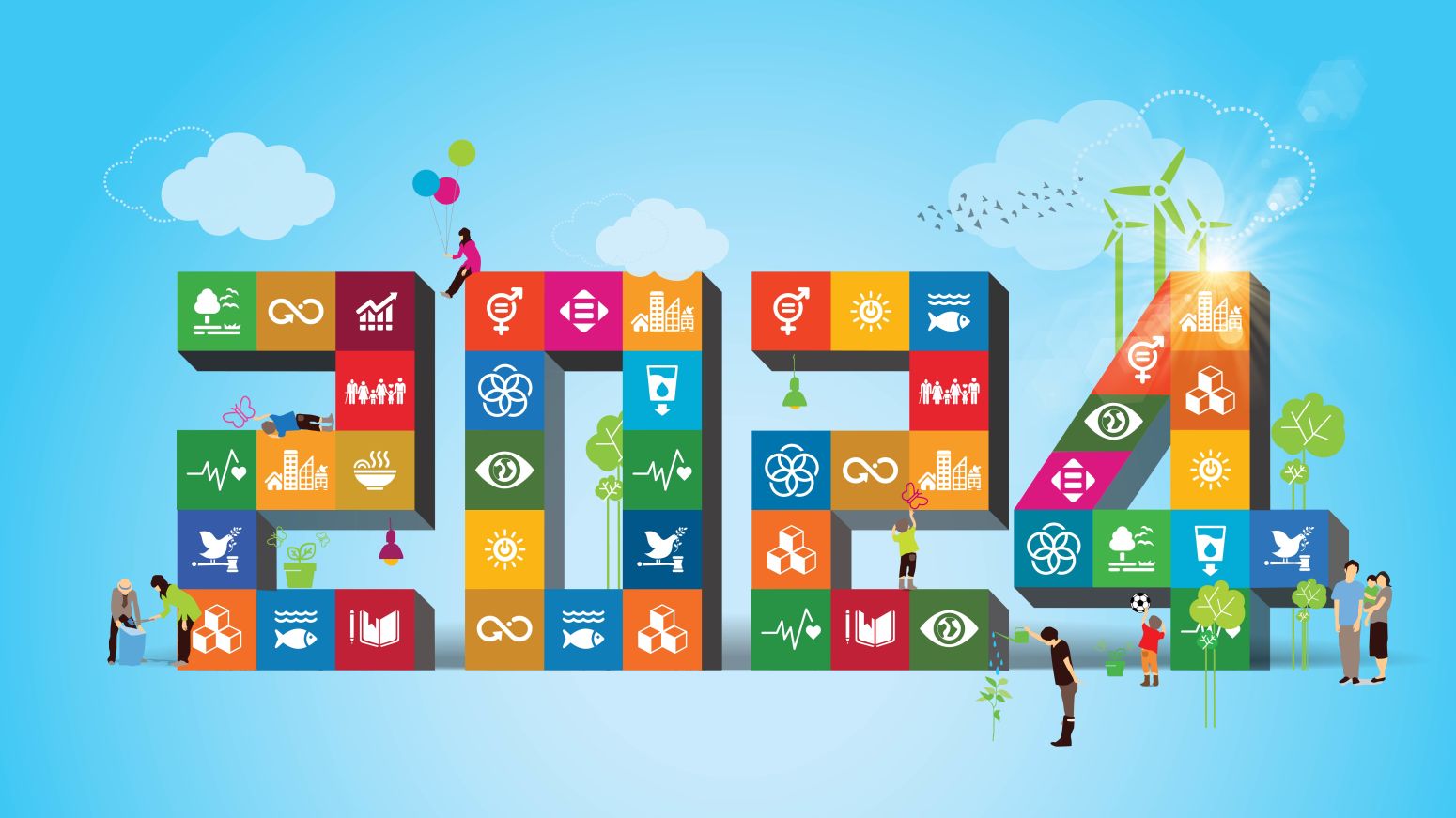
Our values (in addition to our corporate philosophy – see Quality Management Manual, chapter 2) are based on the following five principles:
-
Our knowledge of materials and their properties is combined with a passion for our customers – we combine emotion and function and help them to look good as well as feel good. This applies both to the work of the care staff and to the patients and residents of the facilities. At the same time, we wish to promote a good quality of life for the people who make our clothes and a healthy planet.
-
Responsibility with trust – We value the trust that our customers place in us to do the right thing.
-
Together with other stakeholders in the textile industry, we look to implement change and deliver performance – We work with alliance partners in the Textile Partnership across our business
-
Integrity – We operate under the highest level of ethics and integrity
-
Constant dedication – We never stop asking how we can improve further
-
We work together with responsible partners
We further develop our suppliers in our supply chain based on our assessments and their results.
We implement sustainability together, every day. It is crucial that our staff, partners and suppliers share our values. Our Code of Conduct is integrated into our purchasing conditions (F 0840-06 Purchasing Conditions),and we implement it along the supply chain (where reasonable and feasible) by applying the meta-seal procedure and, where possible, placing orders regionally (at least within Europe).
Our supplier evaluation is summarised in the management evaluation. The Code of Conduct (of the WiBU TextilPlus GmbH) is continuously developed and updated if necessary and applicable. In addition to the Code of Conduct , the terms and conditions of purchase (F 0840-06 Terms and Conditions of Purchase) also include the assessment and handling of violations of the requirements (based on international standards, e.g. ILO).
The Code contains uniform expectations of our suppliers with regard to compliance, labour practices and environmental performance. This is supplemented by our overall guidelines and the requirements from operational business. The Code itself focuses on compliance, yet our approach goes further: We want our main suppliers to implement seals and work purposefully on measures that result from the identified gaps and risks. We support our partners through our involvement in the Textiles Partnership and the exchange and introduction of measures from joint activities. The aim is for our suppliers to continuously improve.
We promote this through the involvement of our staff and constructive dialogue in our flexible teams. The development of competences rounds off this exchange and development of knowledge. This gives them the knowledge they need to deal with and report on key issues that affect them.
If necessary (e.g. in the event of grievances), we will carry out effective analyses. This varies depending on the incident and always includes close communication and cooperation with our alliance partners. For example, we can carry out situation-oriented audits (based on international methods, e.g. ILO) or non-governmental organisations . Examples of well-known NGOs include Greenpeace, Amnesty International and Stiftung Warentest.
-
We base our actions on high standards
Our Code of Ethics for Employees comprises a series of behavioural requirements for our employees. Our managers are responsible for creating a working environment that promotes appropriate behaviour and should lead to exemplary and morally impeccable conduct . Our employees are encouraged to report inappropriate conduct online or by telephone. We use the ' Report button ’ (internal reporting centre) on our homepage and serve as a compliance hotline/fairness channel/fairness portal that both employees and suppliers can use to report violations to the WiBU TextilPlus management team. This forms a committee and is made up of the following groups of people: works council, personnel, management.
-
2.1 Marketing
We wish to develop products that appeal to everyone, regardless of age or size, and we know that this needs to be clear in our advertising campaigns. When we develop new advertising campaigns, we avoid content that could be considered discriminatory, defamatory or offensive. Advertising campaigns are planned in line with the careful preparation of the development of the textiles together with our partners, so that our partners along the supply chain can implement them thoughtfully, taking into account the supporting processes (e.g. production planning) in manufacturing.
2.2 Compliance with human rightsCompliance with human rights is very important to WiBU TextilPlus. Therefore, our Code of Conduct for Suppliers and our Code of Ethics for Employees are based on best practices with regard to human rights, including the UN Guiding Principles for Business and Human Rights and the International Labour Organization (ILO) .
We have reviewed our stance on human rights for loopholes and subjected our purchasing and sales practices to an in-depth investigation. Our aim was to find out how these could affect workers in our supply chain.
2.2 Promotion of fairness and transparencyWe act fairly and transparently and expect the same from our supply chain. With the establishment of our grievance mechanism, which we call ‘Notification’, we can address any issues that arise from situations in our office, warehouse, or supply chain. The results of the feedback are evaluated in this sustainability report, as well as in the management review, with the aim of addressing grievances and successfully implementing measures.
To ensure that all workers in our suppliers' factories are aware of and understand our requirements, our suppliers are obligated to train all their employees and display our Code of Conduct and the contact details of our ‘Notification’ in the local language, f they do not already implement this independently as part of the seals.
The names of WiBU TextilPlus contact persons are clearly displayed on our premises in Ahrensburg, Germany and can be contacted in case of suggestions or questions. We deal with every issue promptly and look for the best solution for everyone involved.
-
3.1 Figures/ dates / facts
-
30 employees
-
More than 100 years of experience in the social market sector
-
€13 million annual turnover
"However, to this day, we define ourselves not by numbers, but by people: our customers, suppliers and employees. We want to continue being a good partner and employer for them through consistency, long-term commitment, and reliability.”
https://www.wibu.care/de-de/ueber-wibu/ueber-uns/geschichte/
3.2 Roadmap - where we stand
Information on opportunities and risks is obtained from various sources, from which we derive measures and define targets in terms of sustainability: we derive our targets from the analysis of the roadmap, feedback from our grievance management as well as from our alliance partners and the research initiated (e.g. ILO). They are divided into binding and recommended targets:
-
binding targets
-
recommended targets
-
targets already achieved
-
targets not achieved, continued
-
freely selectable targets
3.1.1 Policy Statement
Goal Implementation and training on the topics (requirements of the Grüner Knopf) in the individual departments
Goal already achieved ✓
GRI Index: 404-1 | 403-5
Goall : Publication of the topics on the homepage (details from the Policy Statement, details from this Sustainability Report)
Goal already achieved ✓
GRI Index: 102–18 | GRI 102–32
Goal : Certification in accordance with the requirements for the Grüner Knopf and the first products (bed linen, scrubs)
Goal already achieved ✓
GRI Index: 102-21
3.2.2 Anchoring and integration in the supply chainGoal Determination of the requirements of our suppliers by means of (F 0840-07) Supplier Questionnaire and dispatch of the (F 0840-06) Terms and Conditions of Purchase
Goal already achieved ✓
GRI Index: 102-21
Goal Active participation in the Textiles Partnership in the ‘BI Supplier Decarbonisation’ project. It is estimated that the textile industry is responsible for 10% of global carbon emissions. The long-term goal of the alliance initiative is to reduce greenhouse gas emissions in the textile supply chain. Training measures are intended to enable production companies to record their emissions. At least three energy-saving measures should be implemented per company.
Project measures:
-
conducting climate action training
-
creation of factory-specific energy balances
-
advice on defining and implementing measures to reduce greenhouse
-
gas emissions
-
conducting a study on the health effects of air pollution
-
on the local population in the vicinity of the textile production sites
GRI Index:
3.2.3 Identification of the most serious risksGoal : continuous assessment and identification of our most serious risks in our supply chain
Status: The risk assessment for the Grüner Knopf has been completed, however, some of the suppliers’ data are still missing. Nevertheless, an initial overview and prioritisation of our most important risks can be compiled from the available data.
Our largest purchases (37%) are made in Germany (region of Bavaria) and this includes the excellent system in which all legal issues are regulated and comply with ILO requirements. In Estonia, with a business share of 16%, and Portugal (region of Vizela) with 0.5%, the situation is similarly good, although the wage situation is not quite as favourable. The UK, with a share of 4%, is also rather inconspicuous, even though less strict EU laws apply here. In Turkey (region of Denizli), the risks are already significantly higher at 0.5%.
The situation is completely different in countries outside the EU. Our largest partner companies in Pakistan account for 34% (regions of Sindh, Punjab, Karachi, Faisalabad) and China 8% (region of Fujian, Taijiang District). This is where our risks are highest.
We have long-standing business relationships with companies in Pakistan and maintain intensive and constructive dialogue with them. We are delighted that we have been able to deepen and expand our business relationships with the first companies to be recognised in the multi-seal process. We are also pleased that two of these partner companies are also part of our Textiles Partnership working group and are participating in the decarbonisation project (see chapter). Our aim is to successively expand our trust-based cooperation with the aim of strengthening this supply chain.
After the Covid-19 pandemic put our resilience and that of our suppliers to the test in 2020–2021, a devastating flood (10.2022) in Pakistan destroyed the factories and also the homes of our suppliers in this region. Millions of Pakistanis lost their homes and at least 1,700 people lost their lives in the flood disaster.
https://www.bpb.de/kurz-knapp/hintergrund-aktuell/514557/flutkatastrophe-in-pakistan/
Hundreds of thousands of Pakistanis who had to flee from the floods, lived in makeshift shelters. In many places, the electricity and drinking water supply has been disrupted or has collapsed. The impending winter threatened to exacerbate the situation.
The infrastructure has suffered long-term damage, particularly in the provinces of Sindh, where our suppliers operate their factories, Khyber Pakhtunkhwa and Balochistan. An estimated two million houses, almost 400 bridges and around 13,000 kilometres of roads were destroyed, and hundreds of thousands of farm animals died. According to government estimates, the damage to homes, infrastructure and agriculture totalled around 30 billion euros. Crop failures have consequences for the country’s economy and food security that are difficult to quantify. According to observers, half of this year’s cotton harvest, for example, which is a key export for Pakistan, has been destroyed – the jobs of hundreds of thousands of workers in the textile industry are now at risk. Pakistan's government expects the reconstruction to take many years.
https://www.bpb.de/kurz-knapp/hintergrund-aktuell/514557/flutkatastrophe-in-pakistan/#node-content-title-2
GRI Index: 102-21
Note: Cooperation with our partners in China, who officially cover all topics, presents greater challenges. The risks have been identified, but we can only appeal to the government to take legal steps to initiate the implementation of the Supply Chain Due Diligence Act.
3.2.4 Monitoring and reviewGoal : Continuous evaluation of the status of our suppliers' seals and certifications
Status : It will be continuously implemented in the purchasing department after the introduction of the Grüner Knopf.
GRI Index: 102-21
Goal : Continuous assessment of the situation at our suppliers, especially in Pakistan
Status : Assessment of the situation after the fall of the government (04.2022)
After the fall of Imran Khan’s government in April 2022, Pakistan is facing turbulent times in terms of domestic politics. The security situation has also deteriorated. This is because the Taliban takeover in neighbouring Afghanistan has given Islamist extremists and separatist nationalists a boost in Pakistan. In future, we would like to keep ourselves informed about the situation on the ground and work with our suppliers to analyse mitigation options in order to counteract potential effects. These include, for example, food distribution in the factories (see Supplier Questionnaires) and the prevention of labour migration from Pakistan to the Gulf States.
https://www.bpb.de/themen/kriege-konflikte/dossier-kriege-konflikte/54682/pakistan/
https://www.bpb.de/themen/migration-integration/regionalprofile/510100/arbeitsmigration-aus-suedasien-in-die-golfstaaten-das-beispiel-pakistan/
GRI Index: 102-21
3.2.5 Grievance and remedyGoal : Ensuring the legal compliance of our grievance mechanism
Goal already achieved ✓
GRI Index: 102-21
Goal: Establishment of the possibility for continuous feedback from interested parties
Goal already achieved ✓
GRI Index: 102-21
Note: Source of the whistleblower system (WiBU Group): https://www.wibu.care/de-de/ueber-wibu/
The internal reporting office was implemented in Q2/2024. No grievances have been addressed since the introduction of this system. Neither internal nor external grievances were forwarded to the law firm.
Goal : Ongoing evaluation of the grievance mechanisms
Status: Will be implemented continuously following the introduction of the Grüner Knopf. We are receiving legal support for this.
We are proceeding according to the guidelines of CSR Europe, which are based on the framework of the ‘CSR Europe’s Collaborative Project on Sustainable Supply Chains, Business & Human Rights’. The ‘tandem system’ for utilising the legal entity is described here, see ‘UN Guidance Principles and Grievance Mechanisms’ (see introduction, page 4).
GRI Index: 102-21
Goal: Ensure that vulnerable groups are aware of the grievance mechanism
Status: The ‘Internal Reporting Office’, including whistleblower protection, is linked to a law firm that records and categorises the grievances before the issues are forwarded to us.
Access should be ensured for employees in the factories, e.g. training should be provided and access to this contact should be granted. Access should also be ensured for all vulnerable groups who are unable to read. We coordinate this with our suppliers (see also process "P 1020-01 Grievances"), as a notice (even in the local language) may not always be the most effective approach. We want the grievance mechanism to be effective. It is effective when we meet the requirements and it is:
-
1.
legitimate
-
2.
accessible
-
3.
predictable
-
4.
equitable
-
5.
transparent
-
6.
compliant with the law
-
7.
a source of continuous learning
-
8.
based on commitment and dialogue
GRI Index: 102-21
Note: Only after the introduction of the grievance mechanisms can the ‘5.1.2 Backup grievance mechanisms’ be identified.
Grüner Knopf Requirement:
Based on the overview and identified gaps (5.1.1) regarding existing backup mechanisms, the company has identified areas for improvement and:
- reviews participation in existing effective mechanisms and/or
- works on improving existing mechanisms and/or
- explores opportunities to develop new mechanisms in collaboration with external stakeholders. Potentially affected parties and/or their legitimate representatives are involved.
The development and/or improvement of these mechanisms is designed to make them effective (5.1.1).
Note: External stakeholders can include, for example, suppliers, civil society, trade unions, other companies, as well as industry and/or multi-stakeholder initiatives.
-
-
4.1 Memberships and standards
2021
ISO 9001 - Quality with a system
-
The WiBU TextilPlus quality management system was certified in accordance with ISO 9001:2015 by DEKRA . ISO 9001 is the most important national and international standard in quality management. It forms the basis for our continuous internal
2022
Partnership for sustainable textiles
-
As a member of the Partnership for Sustainable Textiles, WiBU Textil has committed itself to actively participating in the Partnership’s overarching goals in an implementation-oriented manner: to demonstrably improve social, economic and ecological conditions along the entire supply chain of the textile and clothing sector. Status: Onboarding process
-
WiBU is part of the ‘ Decarbonisation of suppliers ' working group
2023
-
Analysing the requirements of our suppliers in order to be able to participate in a multi-seal process. Determining and forwarding the requirements of the Grüner Knopf to our suppliers
2024
-
Completion of the introduction and implementation of the requirements of the Grüner Knopf certification
4.2 Further projects are plannedCSR Standard
2024
Starting in 2026, we will present a newly structured sustainability report (according to the Corporate Sustainability Reporting Directive) to the public. We are already working on this in the WiBU Group. Note: An external audit for the introduction and implementation is not planned
Reporting standard
2024
In future, a digital sustainability report is to be set up and expanded on the homepage in accordance with the GRI Standards ‘Core’ option. The content of the report was determined according to the materiality and relevance of the topics in accordance with the requirements of GRI 4.
Grüner Knopf products
2024
Awarding the first products with the Grüner Knopf in cooperation with our suppliers that fulfil the requirements of OEKO TEX Made in Green and the StEP certification as part of the multi-seal process.
Establishment and expansion of sustainability efforts
2025
Every idea counts:
Sustainability Forum founded
The Sustainability Forum was founded to identify approaches for greater sustainability throughout the company, promote dialogue and implement ideas more quickly. The sustainability coordinators of our divisions and teams meet regularly and focus on a specific topic. We wish to gradually review all areas of the company, define new projects, and implement them holistically with maximum efficiency.
This could be part of our contribution to the WiBU Group’s sustainability campaign.
2025
Inclusion of the 17 UN Sustainable Development Goals in our documentation and presentations on the homepage
-
-
Our sustainability goals are part of the company’s quality objectives.
-
Establishment and expansion of our own sustainable textile line, which is labelled with the Grüner Knopf
-
Expansion of the number of suppliers who can implement the meta-sealing process
-
Utilisation and active participation in the sustainability efforts of the Textiles Partnerships
Reporting period:
In future, the information provided in this digital Sustainability Report will refer to the last three years or, for this first report, to the last financial year, as we will be able to present valid figures for this period under review with the introduction of the requirements, in particular ensuring supplier integration, up to and including 08/2024.
-